ANATOMY OF THE APPARATUS BAY
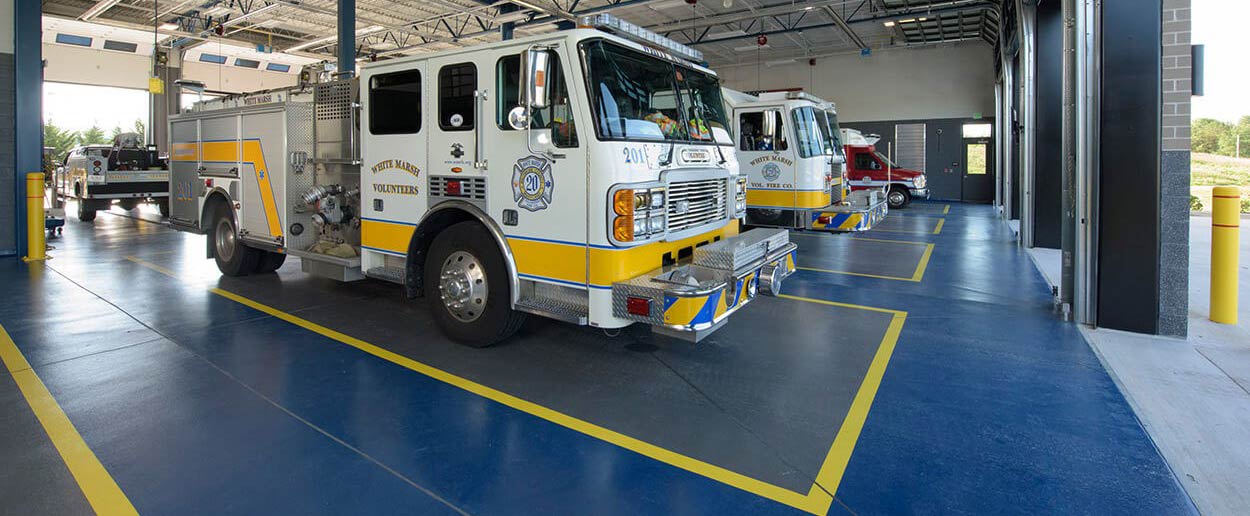
When fire department leaders and architects are tasked with designing a fire station, they should be well prepared to respond to uninformed criticism from the public. During budget hearings, bond referendums, and community input meetings, perhaps one of the most common remarks made is, “It’s just a garage, it shouldn’t cost that much!” Being positioned to respond to such a comment can be the difference maker in the success or failure of gaining project approval.
While fire stations consist of many spaces beyond the bays, apparatus storage space is almost always the largest component. Three key factors have come to influence the design of apparatus bays that differentiates them from the common garage. First, firefighting apparatus and equipment have substantially evolved within the past decades. Equipment size has significantly increased throughout history, and innovation continues to occur. Second is the advent and continued development of building codes. Officials throughout the country have come to realize that fire stations and other essential facilities, such as police stations and hospitals, are critical to the service of the community, and that they must be protected from hazards that might take them out of service. Third, the advancement of construction materials and methods has changed the landscape of the way buildings are constructed. Newer materials are capable of longer spans and can achieve high levels of durability, fire resistance, and improved energy performance.
When fire department leaders and architects are tasked with designing a fire station, they should be well prepared to respond to uninformed criticism from the public. During budget hearings, bond referendums, and community input meetings, perhaps one of the most common remarks made is, “It’s just a garage, it shouldn’t cost that much!” Being positioned to respond to such a comment can be the difference maker in the success or failure of gaining project approval.
While fire stations consist of many spaces beyond the bays, apparatus storage space is almost always the largest component. Three key factors have come to influence the design of apparatus bays that differentiates them from the common garage. First, firefighting apparatus and equipment have substantially evolved within the past decades. Equipment size has significantly increased throughout history, and innovation continues to occur. Second is the advent and continued development of building codes. Officials throughout the country have come to realize that fire stations and other essential facilities, such as police stations and hospitals, are critical to the service of the community, and that they must be protected from hazards that might take them out of service. Third, the advancement of construction materials and methods has changed the landscape of the way buildings are constructed. Newer materials are capable of longer spans and can achieve high levels of durability, fire resistance, and improved energy performance.
#1: Evolution of Apparatus
A little more than a century ago, firefighters operated out of stations built as a home for horse-drawn pumpers. As the fire service continued to evolve, so too did the technology for apparatus and fire stations. Few of the stations of that era demonstrated the planning foresight to accommodate the size and weight of future generations of apparatus.
The length and width of fire apparatus have grown exponentially to the point where many departments are forced to order expensive customizations to ensure that the truck can even fit within the bays. The batteries and generators associated with apparatus have increased the electrical requirements for “shore” lining, and the weight of equipment places tremendous strain on the concrete slabs and foundations. Historically, apparatus bays were once part barn, part garage. The “mechanical” function has since evolved from clearing manure to evacuating carcinogen-laced vehicle exhaust.
With the continued advancement of apparatus design, many departments are faced with the challenge of operating a modern-day fleet of equipment from buildings more than 50 years old. As technology and automation continue to develop at a rapid pace, departments should do their best to forecast what the next 50 to 100 years of apparatus design might look like. Be sure to plan for maximum flexibility. If you think drone response is farfetched, just remember, the guys chasing a horse down the street never dreamed of a 107-foot tiller.
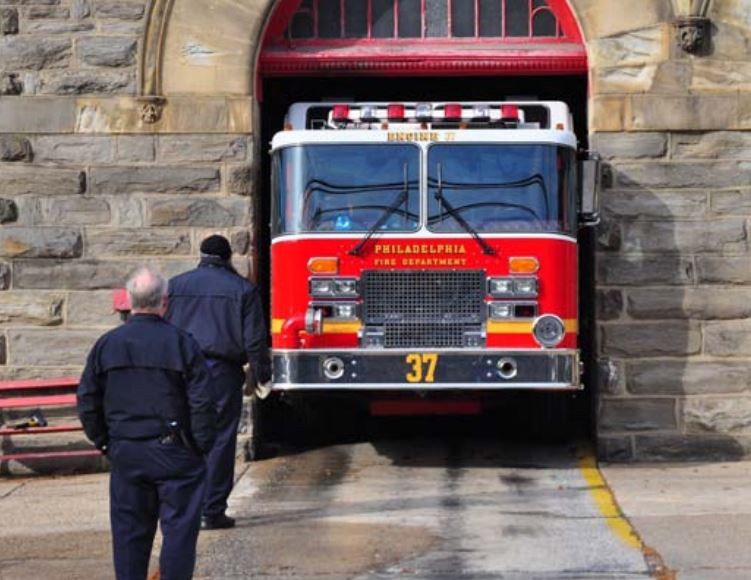
#2: Building Code Development
Events such as the Chicago fire (1871), the San Francisco earthquake (1906), and Hurricane Andrew (1992) decimated and paralyzed communities. In the United States, such natural and manmade disasters have prompted the continual development of building codes to ensure that all types of structures are designed to meet a minimum standard to protect the life safety, health, and overall wellness of occupants. Today, commonly adopted building codes, such as the International Building Code (IBC), designate fire stations and emergency vehicle bays as essential facilities. This classification requires them to be constructed in a fashion that enables them to withstand strong winds, heavy snow loads, and seismic activity to ensure that a widespread event does not sideline emergency responders.
Additional codes and standards further subject apparatus bays and fire stations to unique design requirements. For example, NFPA 1 requires that all new fire stations, regardless of size or usage of materials, be protected throughout by an automatic fire sprinkler system. Such regulations ensure that the building is protected should a fire occur while the department is active on a scene, or that personnel are protected should a piece of apparatus catch on fire while they sleep in their bunks. NFPA standards 1581 and 1500 address issues regarding first responder health by establishing requirements for treating vehicle exhaust and infectious disease control.
In short, for the good of a community, fire stations, and apparatus bays must be designed to be stronger and better protected from natural disasters, manmade disasters, blood-borne pathogens, and carcinogens than most other types of buildings. These codes and standards, among others, directly impact the design and costs associated with the structural, mechanical, electrical, and plumbing systems of the bays, and render them unique from any other building type. It should be expected that continued research surrounding cancer and cardiac arrest in the firefighting community will ultimately spark additional provisions that further impact the financial costs of these essential facilities.
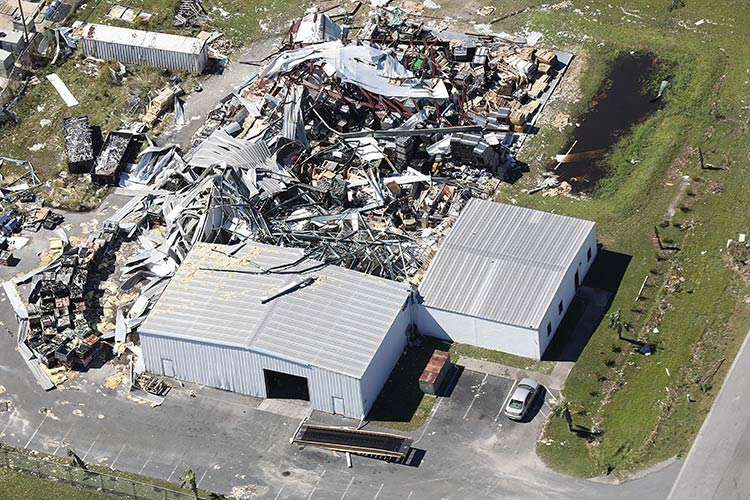
#3: Building System Technologies
Today, apparatus bay designs take advantage of modern building systems to ensure optimal preparedness and energy efficiency. The combination of technology, construction methods, and systems that goes into these spaces is unique from any other building. Understanding the fundamentals of each component and recognizing that they are interwoven to create a cohesive structure is essential, as these systems are what truly sets apart the apparatus bay from a garage.
Exterior walls and structure: Tall unbraced walls and columns have a natural tendency to want to deflect and buckle from the loads carried from above. Additionally, large openings, such as those that occur at the apparatus bay doors, tend to create conditions where the building will be subject to a phenomenon known as structural shear “racking” wherein the end walls are prone to falling into one another like dominos. Such issues are not exclusive to fire stations, however, given the height and size requirements of most bays, a stout reinforcing and lateral bracing system is often required to develop a safe and code-compliant structural design that can withstand severe weather.
Apparatus bay slabs: The structural apparatus bay slab must support the load of equipment and is largely dependent upon good soil conditions at the site. Slabs are often substantially thicker than what might be found in conventional construction. When evaluating potential sites, be sure to conduct preliminary geotechnical studies early in the process to ensure that the soils can support the load of the apparatus.
Floor drainage: Ideally, bays should be designed with a gently pitched slab design that conveys any water to a trench drain located under each piece of equipment. Locating a continuous trench drain under the centerline of each piece of equipment provides several key advantages:
- Water draining from the apparatus is kept away from walking paths thus reducing the risks of slips and falls.
- Wheel points are nominally at the same elevation reducing stress on vehicle suspension.
- Vehicles are not required to contact the drains, thus reducing the wear and tear on the drain covers.
Artificial lighting: Artificial lighting has made tremendous strides in the past 10 years. Departments should consider high bay LED or T-8 fluorescent fixtures with instant-on capability as “payback” periods are often very short. Positioning the lights between the apparatus will ensure that parked apparatus do not cast shadows on walking surfaces. If overhead infrared radiant heat is being utilized, be sure to carefully coordinate fixtures outside of the heater combustibility zone. As with most systems, interoperability with the station alerting system is also now possible. Departments might consider wiring the controls to the bay lighting to a relay for the alerting system so that lights are automatically turned on when a call is received. If washing and maintenance operations are taking place inside the bays be sure to specify damp-proof fixtures.
Natural lighting: Clerestory windows and skylights can be utilized to flood the apparatus bay with natural light, significantly reducing the costs associated with providing artificial light. Light fixtures can be wired to dimmers and control devices that monitor the amount of natural daylight entering the space. When sufficient natural light is available the lights will be dimmed or turned off.
Heating systems: Heating the apparatus bay is crucially important to maintain occupant comfort and equipment functionality. Radiant heat is ideal for all instances as it allows the building to efficiently recover from the cold air that may rush in from an open bay door. Radiant energy is stored in objects or thermal mass (concrete slab), which then radiates heat into the surrounding space, thus warming the environment. The energy is stored in the slab, rather than in the air allowing the space to quickly recover.
Two primary forms of radiant heat function well within the bay environment: overhead infrared radiant and in-floor radiant heat.
Overhead radiant heat requires careful coordination of the unit location to ensure objects that are subject to combustion or damage are kept outside of the specified clearance requirement. Units should be located so that the radiant energy “hits” the floor and not the apparatus.
In-floor radiant heat utilizes pipes or tubing located within the apparatus bay slab to convey warmed liquid through the bays. Heat is typically generated at a boiler and the system can be utilized via a manifold to melt snow and ice on aprons and sidewalks. Careful quality control during construction must take place to ensure damage does not occur to the piping during the cutting of control joints.
General exhaust systems: In many circumstances, regardless of vehicle exhaust systems, building codes require that apparatus bays be ventilated with fresh air. Advanced and cost-effective sensors can detect a wide range of unhealthy gasses, inclusive of carbon monoxide. When quantities reach unsafe levels, fresh air intake, and exhaust fans are activated to “exchange” the volume of air in the building with fresh air. Intake fans or motor-operated louvers provide fresh air at lower elevations and are then exhausted high to achieve a complete cycle. The system can also be manually activated to assist with air circulation on hot days.
Vehicle exhaust systems: Vehicle exhaust is a serious health hazard for first responders and codes and standards require that it be addressed. Numerous systems exist and are heavily debated amongst vendors, departments, and design professionals. Each type of solution presents its own unique advantages and disadvantages. HEPA filtration-type systems provide a clean look and can accommodate any type of apparatus, but they are not necessarily direct source capture and require filter replacement. Hosed connections capture exhaust at the source but can present maintenance challenges associated with connections and can clutter the bays with hanging hoses. Vehicle-mounted systems capture exhaust at the source but do not necessarily solve the problem if the department expects fill-in or reserve units to be used. In any case, vehicle exhaust systems are critical to the health and well-being of first responders. Each department should carefully evaluate the selection of its system with its design team to ensure that it fits their operational vision.
Air circulation: Large industrial fans can supplement HVAC systems during both the heating and cooling seasons to achieve occupant comfort in the bays. High bay structures, such as apparatus bays, tend to experience air stratification where hot air collects at the top of the bays. Low-speed, high-volume fans help to de-stratify the air and improve air quality and overall comfort. During the winter months, the fans can work to mix high temperatures found at the ceiling with the lower temperatures on the floor, creating a more energy-efficient heating system.
Doors: Many conventional and unconventional apparatus bay door options exist. When evaluating doors, consider cost, impact on other construction systems, energy efficiency, speed, security, life span, aesthetics, and safety. Every door type has unique building height/depth clearances and construction requirements. When considering costs, be sure to evaluate the “entire” costs. How will the door selection impact the length and height of the bays and what are those associated costs? What is the life span of the door system and how much should the department plan on spending on maintenance? While sectional doors function well and typically provide a lower installation cost, it may be a better long-term financial decision to invest in costlier four-fold doors that might provide a better insulation value and lower maintenance.
Floor and wall finishes: Consider utilizing quality resinous epoxy floor coating systems that resist staining, increase visibility, improve sanitation, and increase safety through slip resistance. Lines, markings and custom floor graphics can be added to most floor finish systems to improve driver safety. Utilizing high-performance coatings instead of paint on the bay walls will provide a durable finish that is capable of resistance to moisture, chemicals, high heat, and abrasive cleanings.
Structural protection: Protect structural columns and piers with sacrificial elements, such as bollards, to prevent accidents that can cause catastrophic collapse. Bollards should have a highly visible color and should protect the jambs of openings by overlapping the edge of the opening. When designing exterior lighting, be sure to illuminate the columns between doors with light to make it easier for drivers.
Additional infrastructure: Additional infrastructure is typically required to support apparatus operations. Elements may include retractable power reels, air reels, and water reels. Coordinate and locate these reels with the requirements of your apparatus while still leaving enough flexibility for future equipment. Another consideration, allowed by some jurisdictions, is to provide an overhead fill line that is connected to the fire line before the meter. Such a configuration can allow the department to fill equipment from within the building after returning a call. Be sure to coordinate the weight of a fill line with the structural system.
Alerting systems: Alerting, access, and surveillance systems can be integrated throughout the entire building and keep first responders safe, aware of their timing and inform them of call information in an accelerated manner. Integrating the system throughout the bay can also assist in keeping the apparatus area safe.
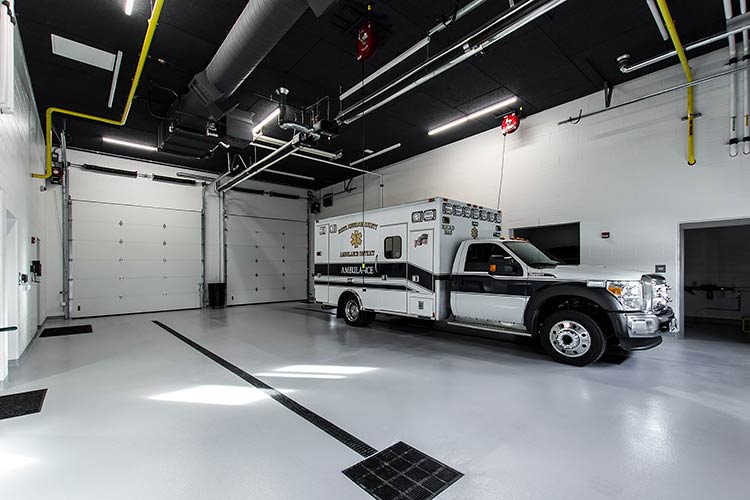
Not Just A Garage
So, no, the apparatus bay is not just a garage; it is far more complex. It is a space like no other, that is vital to community safety. It is a space exclusively intended for storing and maintaining the most expensive and complicated vehicles on the road, ensuring that they can be quickly and safely deployed on time, every time for those who may need it most.
The mechanical systems, structural design and architectural functionality of the bays are uniquely detailed to give first responders and each piece of apparatus the best chance of success in the most trying conditions. Chances are, your critics’ local repair garage doesn’t have to meet such demanding expectations.
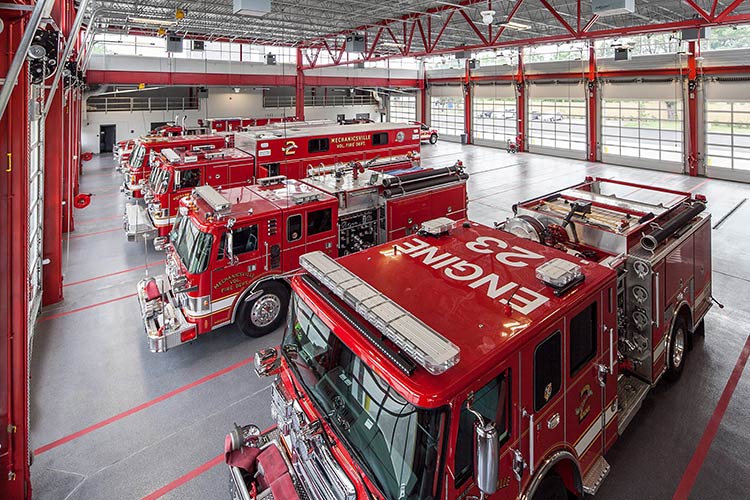
TAKE ADVANTAGE OF OUR DRIVEWAY SEALCOATING & GARAGE FLOOR COATING BUNDLE
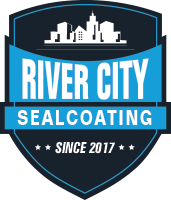
Services
Driveway Sealcoating
Garage Floor Coating
Asphalt Maintenance
Commercial Flooring
Corporate Office
11262 Kilmer Rd
Edison, NJ 08872
Phone
NJ (732-524-7757
VA (804) 234-3180
Recent Comments