TRANSFORM
THE BLAND INTO BEAUTIFUL
Give Your Floors New Life with Aesthetics & Functionality.
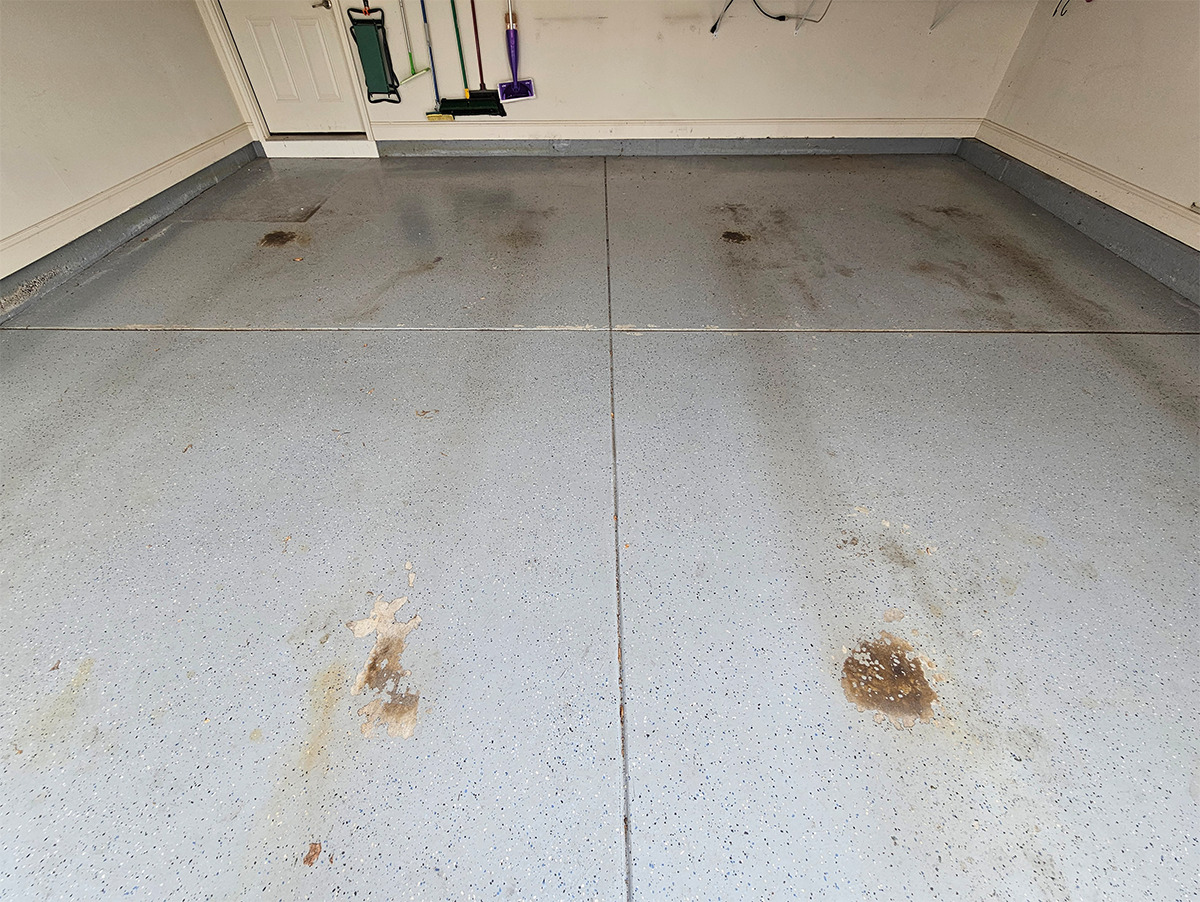
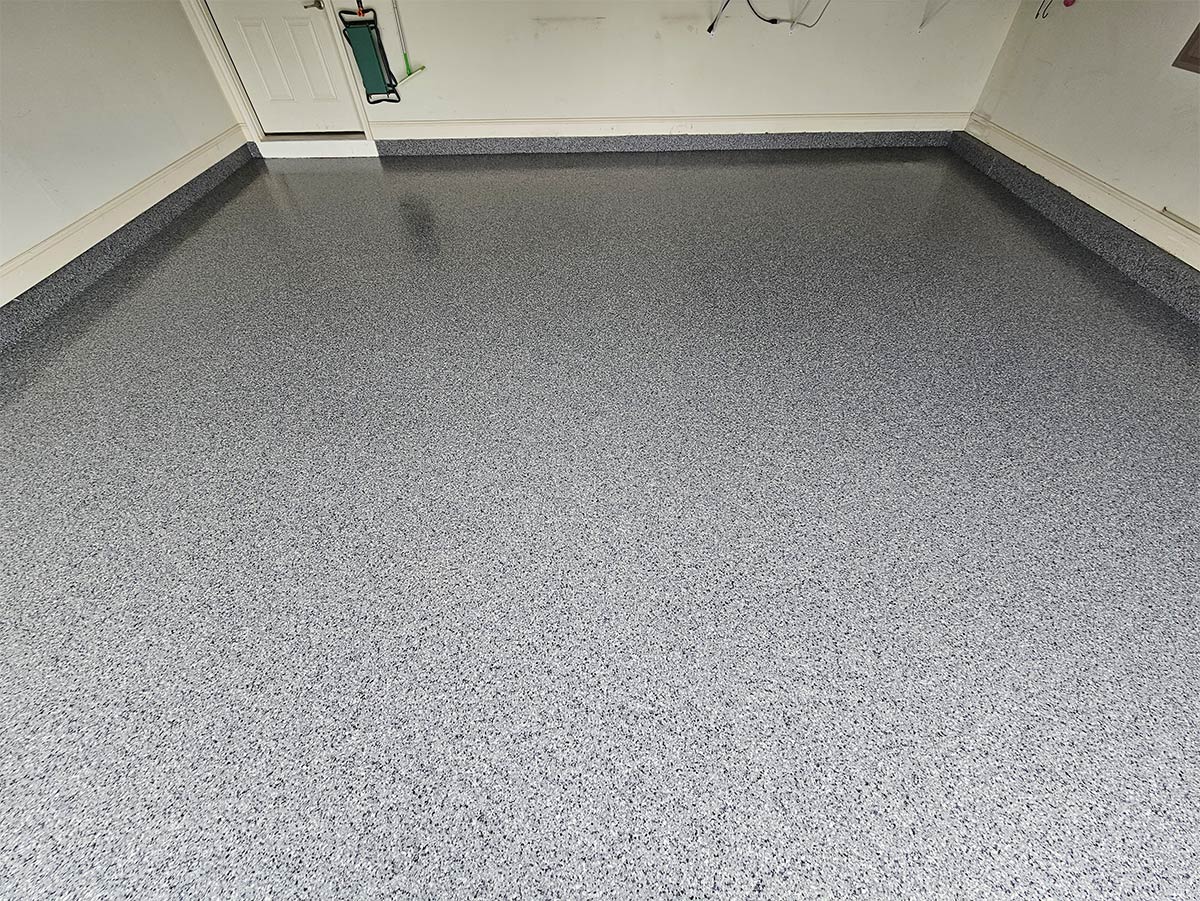
LOVE YOUR FOREVER FLOOR
Your garage isn’t just another room—it’s an extension of your home that reflects your unique style. Throughout the Richmond, VA area, from historic districts near Monument Avenue to modern spaces in Scott’s Addition, garages endure heavy traffic, substantial loads, and exposure to stains, abrasions, and chemicals.
Our residential garage flooring solutions cater to the diverse needs of homeowners across Richmond, VA and its surrounding neighborhoods. Whether you prefer a classic, timeless look or lean toward a more industrial aesthetic, we offer customizable flake finishes and color combinations that blend beauty with durability. Transform your garage into a luxurious, functional space that effortlessly complements your home’s character and withstands whatever life throws its way.
WHY SEAL MY GARAGE FLOOR?
- Attractive. Our expert designers and installation specialists work closely with you to create flooring solutions that perfectly complement the interior and exterior of your home or business. Whether you're enhancing a residential space or a commercial setting, our coatings provide a sleek, polished finish that enhances the aesthetic appeal of any room or area
- Functional. Transform your garage, basement, or any high-traffic area with our concrete floor coatings. Designed to be both durable and stylish, our coatings provide a long-lasting, low-maintenance solution that enhances the functionality of any space, whether it's a home office, craft room, or family hangout spot.
- Easy To Clean. Keeping your new luxury garage floor clean is a breeze. Simply use soap and water to remove any messes, ensuring your floor stays spotless with minimal effort.
- Slip Resistant. Our finished surface flakes create a gentle orange peel-like finish on your concrete surface, significantly increasing slip resistance and improving safety.
WHY SELECT RIVER CITY SEALCOATING ?
EXPERIENCE
With over a decade in the coatings industry, we’re a family-owned business committed to delivering results that exceed expectations—not rushing in and out like “one-day flooring” providers who rely on thin base coats. Instead, we use a 4-step coating system designed to last. We begin with a high-quality epoxy primer to fill any imperfections, followed by an intermediate coating that adds strength and stability. Next, we integrate decorative flakes to achieve your desired look, and finally, we apply a durable polyaspartic topcoat for superior protection against wear, chemicals, and weather.
This meticulous approach ensures a thicker, longer-lasting finish that stands up to heavy use, rather than a quick, flimsy coat that won’t stand the test of time. Our dedication to quality is evident in the 100+ five-star Google reviews we’ve earned from homeowners and businesses throughout the Richmond, VA and New Jersey area. Whether it’s your driveway, a commercial parking lot, or a concrete floor, we take the time to do it right—offering long-term value, enhanced aesthetics, and genuine peace of mind.
NOT A FRANCHISE
Unlike national franchise operations bound by quotas, metrics, and strict purchasing agreements, we’re proudly independent and family-owned—right here in the Richmond, VA region. Without the pressure to meet corporate targets or buy from limited suppliers, we can select the highest-quality materials at fair prices. This approach means no cutting corners or hidden fees—just honest, personalized service.
You’re a neighbor, not a number. We’ve built our reputation on trust, craftsmanship, and genuine care for every project. By remaining locally rooted and family-driven, we ensure that each client receives the attention, quality, and value they deserve.
ATTENTION TO DETAIL
While some companies rush in and out within a single day, we invest the time to ensure every square inch of your concrete floor is thoroughly prepared before the application process even begins. Structural cracks, low spots, pockmarks, concrete spalling, and other imperfections are carefully addressed, and we don’t start up our 800lb diamond pad surface grinder until the surface is ready. After grinding, unsightly stains are removed, the concrete is leveled, and its microscopic pores are exposed—primed to fully absorb our polyaspartic coatings.
We don’t cut corners or rush the job. Instead, we allow a full 24 hours of cure time between the first and second coats, ensuring the initial layer sets properly before the next one is applied. This meticulous approach has earned us a solid reputation throughout Richmond, VA and the surrounding community. We take pride in delivering flawless results—no matter how long it takes—so you can enjoy a truly long-lasting, beautifully finished garage floor.
THREE COATS TO RULE THEM ALL
Some companies offer a convoluted, tiered approach—charging extra for each additional polyaspartic clear “finish” coating and promising upgraded warranties if you add more layers. In reality, going beyond the recommended two-coat system is unnecessary and offers no meaningful improvement in durability or protection. According to the manufacturers’ own specifications, the second clear coating is all that’s required for optimal performance.
Overcharging for multiple “extra” coats that use minimal material and minimal time is simply not ethical. Unlike the “one-day garage” services that pile on every layer in a single afternoon and rush you out the door, we take our time. We allow a full 24 hours between the initial coat and the second, ensuring your polyaspartic floor fully cures and sets as intended.
This careful, honest approach has made us a trusted name in Richmond, VA and beyond. With us, you get precisely what you pay for: a high-quality, long-lasting finish—no gimmicks, no shortcuts, and no needless layers.
OUR PROCESS
Our garage transformations take a minimum of two days, ensuring the meticulous preparation, application, and curing time your floor needs for long-lasting results. Larger or more complex projects may extend beyond this timeframe, but we never cut corners. Before we begin, we’ll conduct a thorough walkthrough, discuss color options, and finalize a plan tailored to your preferences.
Once your design is set, we’ll schedule a convenient date and get to work. Serving homeowners throughout Richmond, VA and the surrounding areas, our process puts quality, communication, and your satisfaction at the forefront—every step of the way.
Step 1: Surface Grinding & Preparation
We start with a 900lb surface grinder, carefully removing about 1/16″ of the concrete’s top layer to eliminate stains, imperfections, and any raised areas resulting from structural repairs. Smaller grinders then tackle corners and tight spots to ensure every inch of your floor is addressed. After the dustless grinding process, our high-powered vacuum system clears away all debris, creating a smooth, contaminant-free surface ready to fully absorb our coating materials.
This meticulous preparation is the same whether you’re in Richmond or in surrounding counties like Chesterfield, Amelia, Goochland, Henrico, Hanover, New Kent, Charles City, or Prince George. We set the stage for a long-lasting, high-quality finish, no matter where you call home.
Step 2: Repair Cracks, Spalls & Other Surface Damage
With the concrete “whitecap” now exposed, we begin repairing cracks, spalling, pitted areas, low spots, and other imperfections using a two-part polyurea crackfill material. This thin, fluid substance seeps deep into the concrete’s pores, ensuring a robust bond. Within minutes, it hardens, fusing the repairs together. A final pass with a 7″ surface grinder brings the restored sections perfectly flush with the rest of the floor.
Whether in Richmond or the greater Central Virginia area, this thorough repair process ensures your garage floor is structurally sound and ready to receive a premium finish that lasts for years to come.
Step 3: Apply Epoxy Primer, Epoxy Intermediate Coat & Decorative Flake Selection
With the surface fully prepped, we start by applying a 93% solids epoxy primer coat, which penetrates deeply into the concrete and fuses the base layer for maximum strength. Immediately following this primer, we add a 100% solid, high-build epoxy intermediate coat, creating a robust foundation for your decorative flake selection. This multi-layer approach provides a far more durable base than the thin, single polyaspartic coat many “one-day” installers rely on.
Serving Richmond and the surrounding region, we take pride in delivering a superior, long-lasting finish that outperforms lesser methods—ensuring your floor stands up to heavy use and maintains its beauty for years to come.
Step 4: Apply Slow Cure, High Build Polyaspartic Topcoat
The following day, we return to scrape and vacuum away any excess flakes, then apply our signature polyaspartic topcoat. We use a slow-cure, high-solids formula, ensuring a thicker, more even layer. Lower-solids products must be applied more thinly and often leave too much texture, trapping dirt and making the surface difficult to clean. They can also result in a blotchy, uneven finish that detracts from your floor’s appearance.
By investing extra time and care, our process ensures a smooth, easy-to-maintain surface that looks consistently great—whether you’re in Richmond, or any of the surrounding communities throughout Central Virginia.
POLYASPARTIC VS EPOXY COATINGS
Polyaspartic Garage Floor Coatings
Polyaspartic is a specialty coating product, derived from modified polyurea in the 1990s, known for its rapid cure time. This two-component system can be walked on within about an hour, yet requires a full 48–72 hours before it’s ready for vehicles or lifts. Highly scratch-resistant, chemical-resistant, and UV stable, polyaspartic coatings won’t discolor under the sun’s rays—making them suitable for both indoor and outdoor applications.
Another key advantage is the coating’s slight flexibility. This adaptability is especially valuable in regions like Richmond or neighboring counties such as Chesterfield or Henrico, where seasonal temperature changes cause concrete surfaces to expand and contract. By adjusting to these subtle movements, polyaspartic coatings maintain a seamless, durable finish that stands up to the demands of everyday use.
Epoxy Garage Floor Coatings
While epoxy coatings are popular, relying on epoxy alone may not deliver the level of durability and protection homeowners in Richmond and surrounding areas need. Epoxy tends to be softer and more prone to scratches, as well as yellowing under intense UV exposure—a common issue for garages that receive ample sunlight or endure heavy use.
These coatings may also struggle with the wear and tear from hot tires, chemicals, and other common garage hazards. For a longer-lasting, more resilient surface, we’ve found that combining epoxy and polyaspartic coatings yields the best results. By blending these two approaches, you create a garage floor that’s not only attractive and resistant to everyday damage but can also stand up to the region’s changing conditions for years to come.
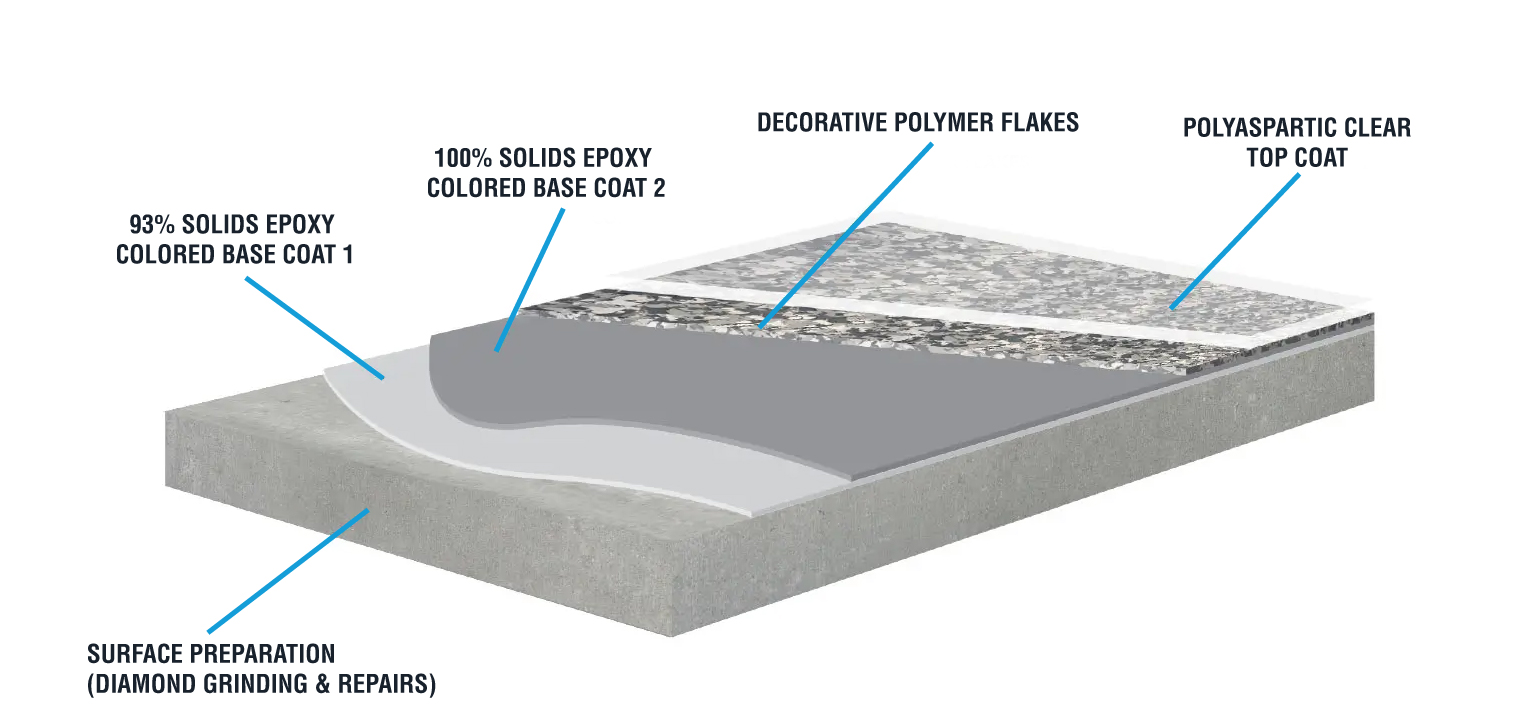
The Sweet Spot
Using epoxy as a base layer beneath a polyaspartic coating offers significant advantages over relying on polyaspartic alone. The epoxy fills small cracks and smooths out imperfections in the concrete, creating a more even surface for the polyaspartic layer to adhere to. This two-part system is highly resistant to abrasion, chemicals, and UV rays, making it well-suited for high-traffic areas—even outdoor applications.
From a scientific standpoint, these coatings chemically bond, forming a cross-linked network with enhanced mechanical properties such as increased tensile strength, impact resistance, and flexibility. In places like Richmond and the surrounding Central Virginia counties, where floors experience temperature fluctuations and daily wear, this combined approach ensures a longer-lasting, easy-to-maintain surface that looks great and holds up year after year.
COLOR FLAKE BLEND SELECTIONS
Whether you’re upgrading a residential garage in Richmond or enhancing a commercial space in nearby counties like Chesterfield or Henrico, color flakes can be custom-blended to achieve the perfect appearance and texture. By integrating color flakes into a resinous flooring system, you’ll enjoy a more vibrant, visually appealing surface that complements your style and withstands the demands of daily use.
The Basics
Color Flake, also known as Decorative Flake, Color Chips, Vinyl Color Chips, or Fleck are specially formulated polymer paint aggregates utilized to improve the aesthetic attributes of resinous flooring systems. It is made up of a combination of acrylic and vinyl resins and generally composed of resin materials, organic minerals, additives, and various pigments. The thickness of a thin flake is typically 4 – 5 mils. Color Flake product is random in shape, sized within a standardized range, and can be also custom blended to reach optimal appearance and texture qualities with a resinous flooring system and match any décor.
Color Choices
Even though choosing a color may seem a simple task or small detail, it may affect the aesthetic of your floor and place. Additionally, the color you choose will affect the maintenance and cleaning practices required to carry out.
The most popular option tends to be a blend of three colors. It is recommended to start with a light color and a dark color before choosing a medium color. So, for example, white, black, and a medium gray tone. Of course, you can use fewer or more color combinations; the choice is yours. There are some websites available that allow you to choose color combinations to see how they would look together, so that may be helpful.
Keep in mind the color of the floor when choosing color combinations. Tan and gray hues are the most commonly used base colors, but many other colors work well too, such as white and black hues. The only time the base color is not important is when you are doing a full refusal, which is when the flakes are distributed over the entire floor until you cannot see the floor color anymore.
Lastly, dirt, dust, grime and spills are an unfortunate inevitability regardless of what room your surface is applied to. Certain flake options are going to show signs of uncleanliness worse than others. It’s important to consider what activities you’ll do on your newly sealed surface and how often you’ll be able to clean it. The classic color for garage epoxy is any of our grey flake options, as these generally require the least amount of upkeep to stay looking great. If you are building a garage gym, we recommend Igneous, as it tends to look like classic gym flooring. While Igneous tends to show dust, home gym owners frequently clean their equipment and flooring to offset this. For our woodworking enthusiasts, we recommend our earthier color options like Saddle Tan, Cafe Mocha or Desert Butte. These colors add a lot of light to the room, make it easy to find dropped screws and nails, and hide much of the sawdust accumulation between cleanings.
The below (12) Colors are the most popular selections and what we constantly have in stock. Visit our Full-Color Selection page to see other custom options available.
Signature Series
With over 75+ different color options including our; Signature, Contemporary, Brownstones, Greystones, Hybrid Stones & Sports Team colors, the possibilities are endless. The colors below are popular trends we’ve seen over the past few years. To see a full list of our color selections, visit our Flake Color Options Page.
Color Flake Profile Size
When choosing a Color Flake design, size matters. Color Flakes are generally available in six standardized size ranges, including: Original (1”), 1/2”, 1/4”, 1/8”, 1/16”, and 1/32”.
Each size profile distinctively influences the appearance of the overall décor to achieve favorable appearance and texture qualities. Larger flake sizes are more random in shape and offer a broad range of dimensions, whereas smaller flakes become more consistent in shape and size as they are reduced.
We recommend using 1/4″ flakes because they can be applied in a single broadcast, cover well and have great strength. Smaller flakes usually require two coats which increases the cost and installation time.
Application & Coverage
We normally recommend Double Broadcast Full Coverage decorative flake system to our customers. With this system, you don’t need worry about the imperfections of the concrete substrate, the pros & cons of different coverage rate, or the selection of base coat colors etc. It’s a proven system that guarantees to give you a beautiful floor with great durability.
- Light coverage – requires .002 lbs per sf.
- Medium coverage – requires .01 lbs per sf.
- Heavy coverage – requires .04 lbs per sf.
- Full coverage – requires .15 lbs per sf.
Color Flake Limitations
Color Flakes are random in shape to provide optimal aesthetics. Flakes sizes could be slightly different from box to box as a result of the manufacturing process, the blending process, and damages during transportation.
Experienced professional installers could notice the difference and avoid uneven distribution while broadcasting. This wouldn’t be a problem for full broadcast systems or even double broadcast systems.
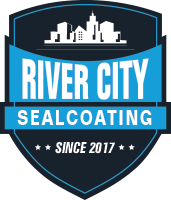
Services
Driveway Sealcoating
Garage Floor Coating
Asphalt Maintenance
Commercial Flooring
Corporate Office
11262 Kilmer Rd
Edison, NJ 08872
Phone
NJ (732-524-7757
VA (804) 234-3180